Discover why you need a high-power fiber laser-cutting machine in your fabrication operations
By Kaylee Swearingen, Marketing Manager at Mazak Optonics Corp.
When you flip through any of the fabrication magazines, you will see advertisements and press releases all mentioning high power lasers. Why is it that the industry wants these higher power levels for laser-cutting?
In 2015, it was common to see 4kW laser-cutting machines at OEMs and job shops across North America. As we are more than halfway through 2019, the trend is a surge for laser-cutting machines powers of 6kw or more. The high power fiber laser category is now approximately 80 percent of Mazak’s laser-cutting sales. But when you look at the benefits of high power, it makes sense why fabricators tendencies are focused in that direction.
High power converts to high yields
There are a variety of productivity and quality benefits that are realized when using higher power levels for laser-cutting. These advancements include an increased cutting range, increased cutting speed, increased piercing speed along with improved part edge quality.
Increased cutting range
A common assumption is that high power means cutting thicker material, which is true. Across the board for all material types, there is an increase in cutting range with higher power. The OPTIPLEX FIBER 10kW laser can cut 1.00” mild steel, 1.25” stainless steel and 1.25” aluminum.
While this increased range of materials is great, another asset that high power allows for is an increased range of cutting using nitrogen and high pressure compressed air. Nitrogen and air cutting not only provide faster cutting speeds but also offer clean parts that are ready to paint and require no secondary cleaning processes.
Mild steel with nitrogen’s cut range increased to ½” with 10kW power but it is also impressive with air cutting. According to Tim Tapper, Applications Manager at Mazak Optonics, “A 6kW fiber laser can cut ¼” mild steel using compressed air, yet with a 10kW’s cutting capability increases to 3/8” mild steel with compressed air.” Air cutting with high power is also giving major improvements in cut quality.
An additional benefit to cutting with compressed air is the ability to reduce your consumables cost since air is much less expensive than nitrogen. Switching to a high power laser utilizing high pressure compressed air reduces operating costs. Tapper stated, “There has been a consistent interest regarding air cutting from our 6kW fiber customers but our customers that are purchasing 8kW or higher, they are all cutting with air.”
But having a larger cutting range is just one aspect of the advantage of high power laser-cutting.
Increased cutting speed and piercing speed
Another gain of high power fiber lasers are the faster cut speeds which increase throughput. High power’s cutting speed is most impactful in mid-range material using air or nitrogen, specifically 1/8” to ½”.
For example, the left side of the photo above shows cutting speed for a single part of 3/16” aluminum. A 10kW fiber laser is cutting 233% faster than a 4kW fiber laser for this single part. If aluminum is not what you process, check out the mild steel example, here.
While a single part speed is impressive, a more relatable reference is running a full nest to show the true overall improvement. Nest times include piercing, fine power ramping on corners, and additional movements that affect the overall cut time of a full sheet.
The right side of the photo shows a full 5’ x 10’ nest of 3/16” aluminum using 4kW, 6kW, 8kW, and 10kW power levels. This nest took 40 minutes and 53 seconds to cut with the 4kW laser. For the same exact nest, the 10kW’s cutting time was only 28 minutes and 57 seconds. With the 10kW you can cut almost an additional half sheet in the amount same time it takes for a 4kW to run the full nest. Check out the mild steel example, here.
Piercing techniques are also being utilized to capitalize on high power lasers’ speed. Tapper explains, “With a 6kW laser, you can pierce 1” mild steel at 3 seconds, but now with the 10kW it is less than a second to pierce through 1” mild steel. This is important for full nest times because if you have a lot of parts or your parts have many features which require many pierces, there will be a dramatic reduction in your nest’s cutting time due to this quicker piercing.”
Speed and throughput are important but so is part edge quality.
Improved edge quality
Since the introduction of fiber laser technology, improving edge quality has continued to be a focus. Fabricators became accustomed to CO2 laser machines offering a fantastic edge quality, to follow suit, solid state laser technology has been striving to achieve the same.
As you progress to higher power levels with fiber lasers, the part edge quality is visibly smoother and cleaner, now more similar to CO2 laser-cut parts. This combination of high power and high speed creates a scenario that dross issues can go away, making the parts edge smoother and cleaner. The improved edge quality with high power is being seen throughout the entire cutting range.
Now which laser-cutting applications see these high power laser benefits most?
Ideal applications
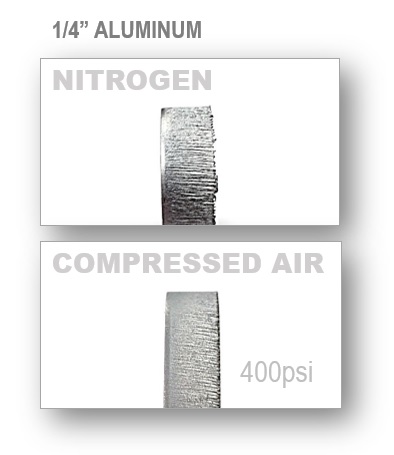
Since high power allows for faster cut speeds in mid-range material, an increased cut range and improved part quality, high power fiber laser machines are ideal for high volume OEM applications and performance job shops.
Applications with longer run times will take advantage of the faster cut rates achieved with higher power lasers. This includes applications where the parts have numerous holes or if the parts are very detailed which requires a great deal of piercing.
Another application that is ideal for high power laser-cutting is thicker aluminum parts. When high power laser-cutting and compressed air are combined to cut aluminum, it offers a superior, smoother edge quality with significantly less dross.
Specific applications situations can be further discussed with your Mazak regional manager.
Conclusion
Overall, high power lasers offer an increased cutting range, the ability to cut thicker with nitrogen and compressed air, higher speed cutting, faster piercing times, and improved part edge quality. All these high power advantages increase laser-cutting throughput and reduce the cost-per-part.
Now the question is, why not high power?